Зроблено в Києві. Як під час війни в столиці почали виготовляти бронежилети найвищого класу захисту
Наприкінці березня підприємець з Донеччини Северіон Дангадзе у власному офісі почав виготовляти бронежилети.
За три місяці він безкоштовно роздав військовим близько 1 500 цих елементів індивідуального захисту. За цей час виробництво розширилося та переросло в повноцінний бізнес.
Зараз у компанії UKRTAC працюють понад 100 людей, а потужності виробництва дозволяють виготовляти близько тисячі бронежилетів і 3 тис кевларових шоломів на місяць.
Як столичний підприємець налагодив виробництво бронежилетів шостого класу, які можуть конкурувати з більш дорогими ізраїльськими аналогами?
Українські бронежилети UKRTAC
Одразу після початку великої війни Северіон Дангадзе записався до територіальної оборони Києва.
Багатьом відомо, наскільки велика тоді була потреба в елементах індивідуального захисту. Мало не кожен тероборонівець купував їх за власні кошти. Тож Северіон почав допомагати з амуніцією.
Перші 100 бронежилетів, які підприємець придбав, були якісні, але дорогі. Наступні коштували ще дорожче і мали гіршу якість, ніж попередні.
Після цього Северіон вирішив заснувати власне виробництво бронежилетів. Жодного досвіду у цій сфері він не мав.
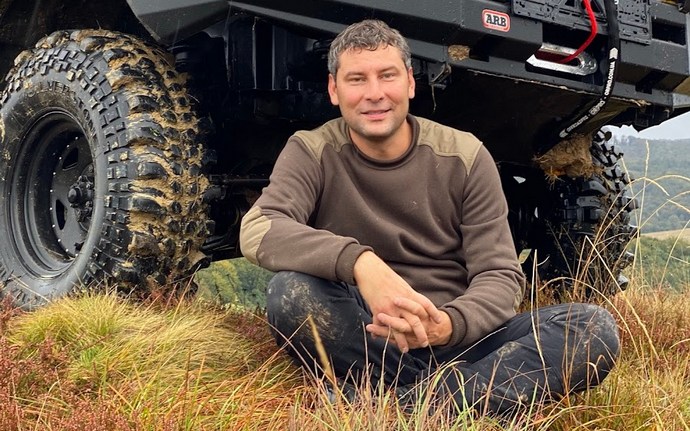
Северіон Дангадзе у 2007 році переїхав з Донеччини в Київ, де займався бізнесом, пов’язаним з інвестиціями в європейські стартапи та ІТ-проєкти.
У 2017 році Дангадзе очолював київський обласний осередок партії "Рух нових сил". Тоді його заарештували за підозрою в державній зраді. Через пів року суд присудив йому умовний термін за співпрацю зі слідством, а у 2021 році його звільнили від покарання.
Ідея підприємця та експолітика щодо створення виробництва бронежилетів почала швидко реалізовуватися.
Першим виробничим майданчиком для пошиття плитоносок став просторий офіс Дангадзе в центрі Києва. Сюди завезли десять швейних машин для роботи з грубою тканиною. За деякий час кількість швачок збільшилася з трьох до десяти.
Першу модель бронежилета постійно вдосконалювали з урахуванням відгуків військових. Так вдалося пошити бронежилет, який за якістю схожий на ізраїльський, але коштує в півтора разу дешевше.
Ізраїльські бронежилети популярні серед українських військових завдяки невеликій вазі (містять керамічні пластини з оксиду алюмінію) та надійності. Четвертий клас таких бронежилетів відповідає шостому за українською класифікацією.
"До кінця червня ми віддавали бронежилети безкоштовно. Загалом роздали понад 1,5 тисячі з плитами шостого класу. Я хотів допомогти і в мене була така можливість", – каже Дангадзе.
Згодом виробництво переїхало в більше приміщення в центрі Києва. У ньому вдалося розмістити 45 швейних машин, а кількість працівників збільшилася до 60-ти.
"Уся команда, крім інженера-технолога, – це люди з різних сфер, які раніше не мали досвіду виробництва військової амуніції. Команда розширювалася більше за ідейними критеріями", – зазначає операційна директорка UKRTAC Ольга Смиковська.
У створення виробництва Дангадзе інвестував близько 1,5 млн дол.
UKRTAC виготовляє бронежилети шостого класу з керамічними бронепластинами, які мають невелику вагу, порівняно із стальними, та вищий клас захисту.
"Держава забезпечує військових бронежилетами з металевими плитами. Вони важкі. Щоб не нашкодити здоров’ю, можна носити на собі до десяти кілограмів не більше чотирьох годин на добу", – пояснює підприємець.
Вага бронежилета UKRTAC у максимальній комплектації – 7 кг, тоді як вага базової версії з металевими пластинами починається з 11 кг.
Керамічні пластини компанія купує в Польщі, а балістичний пакет з них виготовляє в Україні.
"Ми почали шукати технології для виготовлення керамічних пластин в Академії наук та Інституті Патона. Знайшли людей, які знають технологію, але не змогли домовитися із вченими.
Вони спочатку не могли скласти ціну, а потім щотижня її підвищували. Тому купуємо керамічні плити в Польщі, а в Україні виготовляємо з них балістичний пакет, запаюємо його і запаковуємо", – зазначає Северіон.
Кожна партія бронежилетів під суворим контролем проходить відстріл у лабораторії, за результатами якого складається протокол та видається сертифікат якості.
"Ми інформуємо лабораторію, що маємо тисячу бронежилетів. Вони приїжджають, перераховують партію, дістають п’ять плит з різних місць на власний вибір та відстрілюють їх", – розповідає підприємець.
Кожен бронежилет складається з майже 40 деталей, має системи швидкого скидання. Для пошиття використовують тільки оригінальні матеріали. Наприклад – американську запатентовану високоміцну тканину марки CORDURA, яка не світиться в тепловізорі.
Фурнітуру купують в італійської компанії 2М, яка виготовляє деталі для американських та ізраїльських бронежилетів.
"Ми виготовляємо амуніцію лише з оригінальних матеріалів. З цього виходить вартість. Порівняно з українськими виробниками, така фурнітура вдесятеро дорожча, але ми хочемо, щоб якість була найкраща", – пояснює Дангадзе.
Бронежилет шостого класу з боковим захистом та керамічними плитами коштує майже 40 тис грн (930-950 дол). Аналогічний ізраїльського виробництва обійдеться у 1 600 дол.
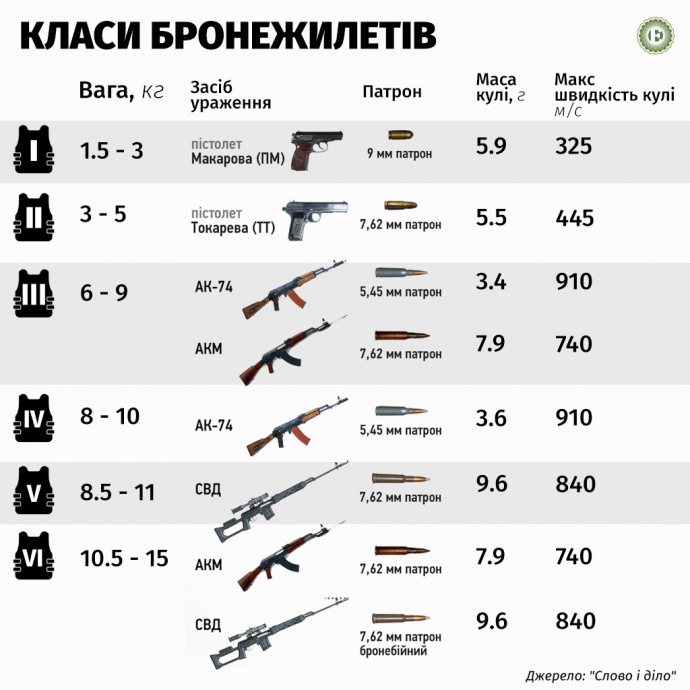
Бронежилетами компанії UKRTAC, за словами підприємця, користуються представники всіх силових структур в Україні: СБУ, ГУР, ССО, "Альфа" і, звісно, ЗСУ.
"У нас ГУР брали 30 бронежилетів, а через деякий час повернулися і взяли ще стільки ж. Підрозділ потрапив у важкий бій, один військовий загинув, дехто отримав поранення, але майже всі вижили завдяки нашим бронежилетам. У такі моменти ми розуміємо, що наша справа рятує життя", – зазначає Смиковська.
Наразі потужності підприємства дозволяють виготовляти близько тисячі бронежилетів на місяць. Аби процес відбувався злагоджено, кожен працівник має покрокову інструкцію з пошиття.
"Коли приходить нова людина, вона шиє один жилет близько трьох днів. Потім протягом тижня вона починає шити один жилет на день. Через місяць вона може шити півтора жилети на день. Багато людей не витримує, бо матеріал грубий, шиється важко, це важка праця", – каже Дангадзе.
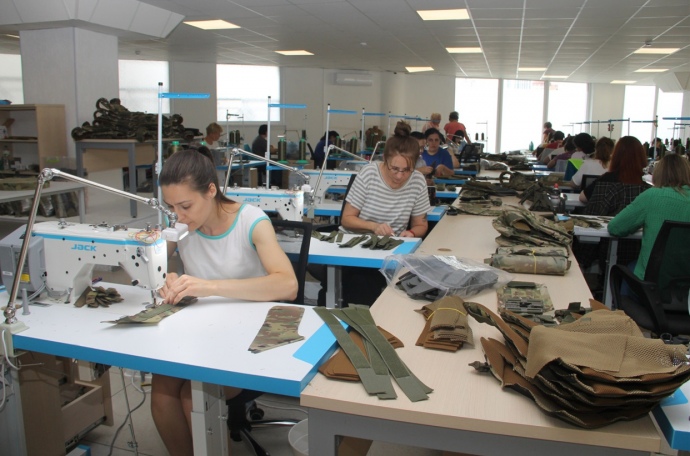
Щоб мати можливість виготовляти військову амуніцію та імпортувати сировину для виробництва, компанії довелося пройти багато складних бюрократичних процедур.
"З документами було важко. Отримати дозвіл на виробництво і сертифікат на бронежилет – це два різні шляхи. Десь допомагали, десь спасибі, що не заважали. Знадобилися три місяці, щоб все оформити", – розповідає підприємець.
Бронежилети пройшли сертифікацію. Їх випробовували в різних складних умовах, наприклад, нагрівали до температури плавлення, заморожували, а потім відстрілювали.
"Спеціально для нашої амуніції розробили технічні умови. Останній документ, який ми отримали, – міжнародний стандарт якості", – додає Смиковська.
Шоломи, виготовлені в Україні
Компанія UKRTAC також виготовляє шоломи, штурмові рюкзаки, підсумки, додатковий балістичний захист.
Автоматизовану лінію з виробництва шоломів виготовили самостійно за 30 днів, бо швидко купити таке обладнання в Україні чи за кордоном не було можливості.
"Купити можна було в Італії або Китаї. Італія нам давала чотири місяці на виробництво, а Китай – три місяці і ще місяць на доставку. Ми вирішили самостійно зробити. За місяць створили програмне забезпечення, автоматику, металеву частину", – розповідає Северіон.
Перші шоломи виготовляли методом проб та помилок, шукали інформацію з відкритих джерел, консультувалися з фахівцями.
"Ми брали кевлар різної щільності, різну кількість шарів. Усе це пробували, відстрілювали, доки не прийшли до ідеалу і зрозуміли, який матеріал нам потрібен. Зараз замовили кевлар, який ще в дорозі", – каже Смиковська.
Виробництво шоломів розділене на кілька зон. Зі складу, де в спеціальних температурних умовах зберігається арамідна тканина (кевлар), вона потрапляє в зону розкрою. Спеціалісти беруть нарізані шматки тканини та викладають у спеціальні чаші під прес.
Далі процес повністю автоматизований: прес при відповідній температурі опускається і на виході отримується сирий "горщик", який потрапляє в кімнату обрізки, а згодом фарбується і комплектується фурнітурою.
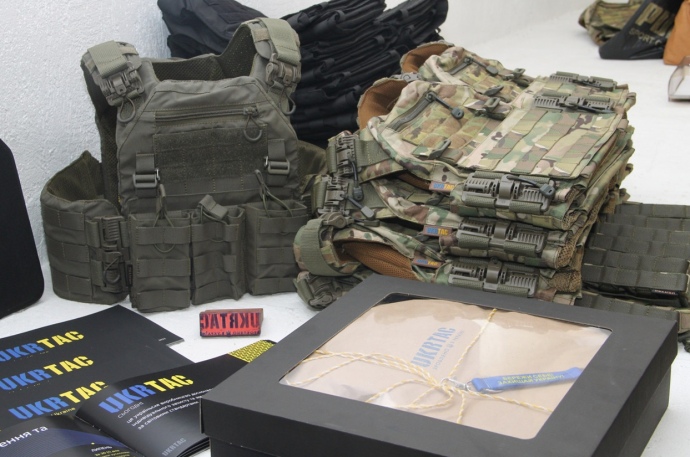
Для виготовлення одного шолома потрібно близько 6 кв м кевлару. Придбати його за кордоном непросто через обмежену кількість виробників та підвищений попит.
"У світі лише чотири-пʼять компаній, які виготовляють балістичний кевлар. Черги на замовлення починаються від року. Щоб купити кевлар в одній з найбільших компаній – DuPont, потрібно сьогодні заплатити гроші і забрати його через рік. Або можна купити завтра, але ціна буде приблизно в півтора разу вищою", – пояснює Дангадзе.
Виробництво шоломів запустили недавно. За цей час виготовили до 100 одиниць. Це тестова партія, шоломи поки не надходили в продаж. Більшу частину з них безкоштовно роздали українським бійцям.
"Після запуску виробництва ми виготовили шоломи, відстріляли їх, отримали позитивні відгуки і тільки потім замовили матеріал", – розповідає підприємець.
Смиковська додає, що відстріл шоломів проводиться в лабораторії під протокол у присутності керівництва і власника.
"Коли ми були в балістичній лабораторії, то бачили багато відстріляних шоломів. Більшість з них проходять випробування, бо куля не пробиває шолом, але в деяких вм’ятина не рятує людину від травм. У нашому шоломі вм’ятина менше допустимої норми", – каже операційна директорка.
Зараз на підприємстві є чотири установки, потужності яких дозволяють виготовляти до 150 шоломів на день або близько 3 тис на місяць. Розміри шоломів регулюються завдяки внутрішнім подушечкам та підтяжкам від М до XL.
Дангадзе зазначає, що за потреби виробництво можна швидко подвоїти або потроїти, бо компанія має досвід і технологію для розробки обладнання.
Про плани на майбутнє
Про перспективи Дангадзе говорить обережно. Мовляв, час покаже, що робити далі. Після перемоги підприємець розглядає варіант експорту продукції.
"Логічно було б спробувати вийти на світові ринки, але про це рано говорити. Ми були в Польщі на одній з трьох найбільших у світі виставок військових товарів.
У нас були клієнти, які хотіли зробити замовлення тут і зараз, але закон забороняє під час війни продавати амуніцію за кордон", – додає засновник UKRTAC.
Смиковська додає, що великих замовлень у компанії ще не було, але UKRTAC має всі документи для участі в держзакупівлях. "Ми абсолютно готові, це питання часу і переговорів", – пояснює вона.
За словами Северіона, виробництво ще не вийшло на точку беззбитковості.
"Цех з виготовлення бронежилетів "тягне" виробництво шоломів, яке не працює, поки нема матеріалу. Якби виробництва були окремі, то ми б мали невеликі прибутки від продажу бронежилетів і повний мінус на шоломах. Але я їх не відокремлюю", – підсумовує підприємець.
Cтаття підготовлена в рамках проєкту "Реформи для свободи українського бізнесу" в партнерстві з Atlas Network